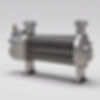
About the Founder
Les Jackowski is a recognized expert in heat exchanger design, troubleshooting, use of anti-fouling coatings, and enhanced heat transfer surfaces. He possesses a rare background that combines strong theoretical foundation with pragmatic engineering solutions. Les is an author and co-author of many high impact patented innovations and technical publications. Les is experienced in leading small groups of engineers to deploy new technologies for heat exchangers and fired equipment. Les initiated and executed multiple projects to improve thermal efficiency and reduce GHG emissions. This program delivered value of $150 MM in energy savings and CO2 credits.

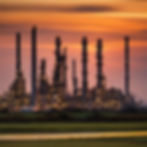
Examples of Projects
Redesigned 10 crude stabilizer reboilers with low density low fin tubes. Impact: avoided $10 MM capital project $1.8 MM/year maintenance savings​,
Redesigned a regeneration gas (25% H2S) heater.  Developed a unique pillow box design for CEU exchangers.  Impact: new design eliminated LPO of $60MM experienced prior to the retrofit. ​
Retrofitted feed-effluent exchangers for NHT with enhanced heat transfer surfaces. Impact: increase in production worth $1.1 MM/year, energy savings of $400K/year, reduction in GHG by 16 MT/day.​
Retrofitted electric process heater (EPH) element bundles to avoid overheating of the shell. Developed new corporate standards.  Impact: trouble-free operation of new heaters.
Deployed groovy fins for an air cooler as part of a modernization project.  Impact: this retrofit allowed to cancel a $2MM capital project to install a new bigger heat exchanger.
Designed a completely new preheat train for 50 K Bbl./day crude unit. The new design increased preheat by 100 F and feed rates by 10%.
Deployed antifouling coatings and dual enhanced tubes for a condensate stabilizer on a production platform. Impact: reduction in fouling rates, increase in production rates, reduction in CO2 emissions. Total value creation of $20MM.
Designed Selective Catalytic Reduction (SCR) systems for process heaters (refineries), boilers (chemical plants), and gas turbines (power plants). The scope included the catalyst selection, design of ammonia (aqueous and anhydrous) vaporizing skids, and ammonia injection grids. Performed factory acceptance tests, and startup troubleshooting. Wrote operating manuals and provided training for operators. These SCR systems reduced NOx emissions by over 95%.
Modified surface condensers in three 200 MW power units. This revamp increased the overall efficiency of the power unit by 3% i.e., increase in power output by 18 MW with no additional fuel burning. 18 MW of power corresponds to energy demand of 10,000 US households.